«Partiamo da questo e lo trasformiamo in quest'altro»: ecco come funziona la stampante 3D
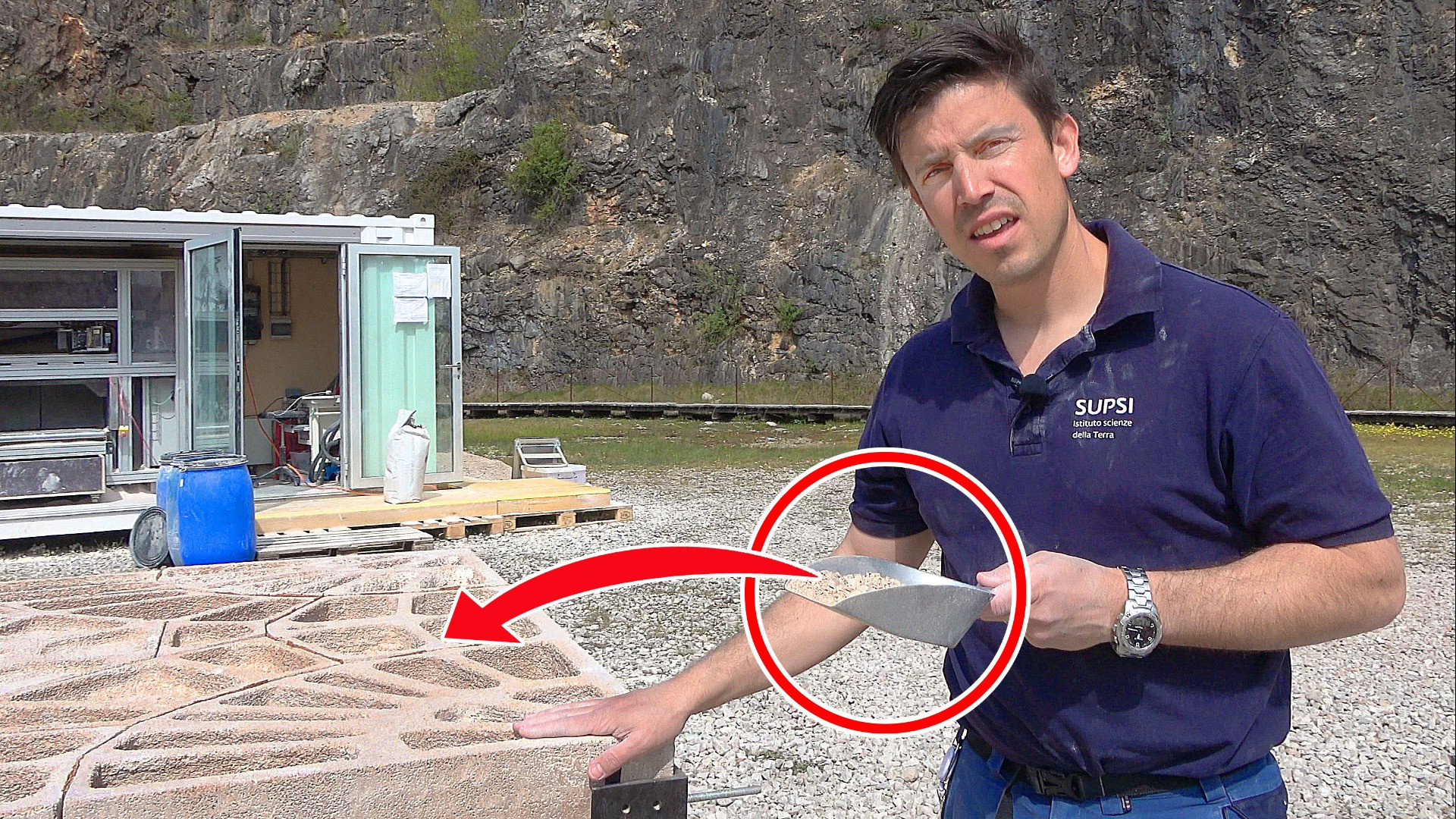
Ve lo abbiamo presentato ieri, quando il prototipo era stato ultimato da pochissime ore. La SUPSI e il Politecnico di Zurigo hanno unito le forze in nome dell'economia circolare: ecco la stampante 3D destinata a rivoluzionare il mondo dell'edilizia. Il macchinario, per l'occasione collocato nella cava di Arzo, ha già trasformato gli scarti di questo luogo in elementi architettonici. «Dal 20 al 40 per cento della produzione è destinato alla discarica», afferma Filippo Schenker, ricercatore dell'Istituto scienze della Terra SUPSI (Dipartimento ambiente, costruzioni e design). Tonnellate e tonnellate di materiale che finiscono subito nei rifiuti. «Fino a oggi, perché grazie a questa invenzione diamo nuova vita a ciò che prima si gettava», ci spiega il nostro interlocutore, a cui abbiamo chiesto di mostrarci il funzionamento.
Il 39.enne spala una badilata da un enorme cumulo ai piedi della miniera attraverso una rete metallica applicata a una cassetta sottostante. Mentre raccoglie una manciata di detriti con un'altra palettina, il piccolo polverone di sabbia e sassolini che si è appena sollevato inizia a disperdersi nell'assolata giornata primaverile. «Partiamo da questo – indica versando una parte sull'altra mano –. E lo trasformiamo in quest'altro», dice gettando i sassolini a terra e picchiando con forza la mano su un'enorme lastra decorata, collocata su un ripiano. «Si tratta di una cupola realizzata con la nostra nuova tecnica». Altri due colpi dimostrano la solidità del prodotto. «Guarda le decorazioni... geometrie e forme si possono personalizzare a piacimento». Ma c'è di più, perché Schenker rivela un altro dettaglio: l'elemento architettonico, nello spessore, ospita molte varie aree vuote. «Abbiamo messo materiale solo nei punti in cui serve, per questioni di statica». Così facendo, non solo si risparmia materiale, ma l'elemento risulta anche più leggero.
Dal Ticino a Venezia
L'opera realizzata con gli scarti della cava sarà esposta alla Biennale di Venezia dal 20 maggio. Un motivo d'orgoglio in più per Pietro Odaglia, inventore del grande apparecchio, e per Vera Voney, ricercatrice del politecnico e oggi collaboratrice dell'azienda Oxara. «Durante il mio dottorato ho iniziato a sviluppare il geopolimero per questa stampante. Abbiamo sostituito il legante organico esistente, che è tossico, con questa nuova formula», spiega la 33.enne. «Durante lo sviluppo di questa tecnologia ho incrociato Filippo, che lavorava con le cave di pietra naturale ticinese. Abbiamo pensato che si potessero introdurre gli scarti di cava in questa nuova stampante. E ha funzionato», esclama con un sorriso. Senza il suo contributo, è probabile che un risultato del genere non si sarebbe mai visto.
Economia circolare, nuove opportunità. Recupero di materiali finora eliminati. Un sogno che diventa realtà e che potrebbe permettere di risparmiare anche svariati milioni di franchi (oltre 350, se si tiene conto del costo attuale dello smaltimento).
Formula magica
Intanto Pietro (un nome che è tutto un programma, insomma), ha terminato i lavori preparatori attorno alla sua macchina, che se ne sta comoda in un grosso contenitore d'acciaio del tutto simile a quelli usati nelle spedizioni navali. Ora è pronta per essere accesa.
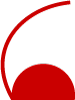
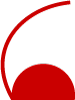
«Non sarà portatile, come siamo abituati a definire un apparecchio tecnologico, ma in effetti può essere trasportata su un cantiere o sul posto in cui si producono scarti adatti a essere recuperati». Un flacone trasparente poco più grande di un bicchiere, attaccato a uno dei pilastri d'acciaio che delimitano l'area di stampa, contiene un primo ingrediente del successo. «Si tratta di un componente che non richiede particolari misure di sicurezza, al contrario di molte resine impiegate in processi simili».
Il 34.enne originario di Genova, dove ha studiato architettura, e oggi ricercatore del Politecnico di Zurigo, indica una tanica sul pavimento e un tubo collegato al serbatoio trasparente. La sostanza, che reagisce con il caolino aggiunto ai pezzetti di marmo di scarto della cava, è risucchiata dalla tanica e alimenta la boccetta. Quando indurisce, il composto non si tramuta in un minerale o in non vetro ma in una via di mezzo, un elemento che all'interno ha delle strutture polimere non plastiche.
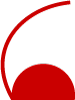
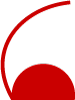
È il momento di accendere
Un paio di clic nel programma per gestire il modello tridimensionale sul computer, che continua a funzionare alla perfezione nonostante la polvere che si è depositata ovunque e non ha risparmiato né schermo né tastiera. I tre protagonisti sono attorno alla creazione che inizia a emettere un ronzio profondo accompagnato da una vibrazione, come le fusa di un grosso gattone. Un primo carrello si muove in orizzontale e stende lo strato di caolino abbinato allo scarto di marmo della cava. «Qui di lato c'è un rullo compressore che schiaccia la superficie sul piano di stampa, la quale misura 80 centimetri per 120». Un altro rumore. Un altro carrello dalla direzione opposta. «Su questo carroponte abbiamo gli ugelli con la testina di stampa, che in realtà distribuisce il collante».
La tecnologia della stampa 3D non è una novità. E nemmeno il riutilizzo di scarti minerali per creare nuovi componenti. «Ma ci abbiamo messo due anni per arrivare a questo risultato, vale a dire ottenere elementi finiti molto più resistenti rispetto ad altre soluzioni in commercio, anche a parità di materiale. Due anni con parecchi esperti e ricercatori che hanno avuto a che fare con ogni aspetto dei problemi che emergono una volta che ci si imbarca in un'impresa simile».
«È un materiale resistente e anche molto bello dal punto di vista estetico, dato che richiama colore e caratteristiche della roccia madre, in questo caso quella del marmo di Arzo», aggiunge ancora Schenker.
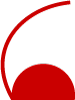
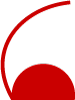
La sagoma emerge dalla polvere
L'invenzione ha fatto centro. La sagoma che prima era soltanto un disegno sullo schermo di un computer emerge piano piano dalla polvere. Per avere un pezzo di cupola simile a quella collocata al centro della cava principale, però, occorrerebbero una dozzina di ore «più altrettante di riposo per asciugare e indurire il blocco stampato», sottolinea Odaglia.
«Abbiamo provato tanti materiali, non solo il marmo di Arzo. Anche gneiss, granito, e scarti di demolizioni da cantiere. Tutti con risultati sorprendenti. Si tratta di residui molto difficili da usare in qualsiasi processo industriale. Di fatto, con questa tecnologia di stampa, si tratta di materia prima che non solo è gratis, ma quasi ti pagano per utilizzarla, dato che il suo destino è la discarica».
Il papà del macchinario immagina un futuro per la sua trovata: «Sì, ma mi serve ancora un mese di lavoro per automatizzare una serie di fasi su questo prototipo. Una volta terminato questo passaggio, il piano sarebbe trovare una realtà che si possa associare affinché questo tipo di tecnologia sia applicata direttamente in un progetto architettonico. Le capacità meccaniche e di resistenza che siamo riuscite a raggiungere sono notevoli. Quanto esce da qui può essere comparato a un calcestruzzo C20/25, quindi si potrebbe utilizzare per svariati ambiti applicativi nel mondo della costruzione».